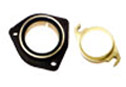
В современной промышленности пеномодели для ЛГМ изготавливают различными
способами. Способ изготовления зависит от масштабов производства и размеров
будущей пеномодели и отливки:
- в единичном и мелкосерийном типах производства, а так же при
производстве крупногабаритных деталей, пеномодели изготавливают методом
механической обработки. Т.е. либо с помощью разогретой нихромовой струны
по шаблонам, либо на станке с ЧПУ из заранее отформованной заготовки полистирола
вырезают требуемую пеномодель.
- при крупносерийном и массовом производстве пеномодели изготавливают в
основном методом теплового удара в прессформах. Для данного процесса так же
необходимы автоклавы или же специализированное формовочное оборудование.
Процесс изготовления пеномодели методом теплового удара можно разделить
на несколько этапов:
1.
Проектирование и изготовление технологической оснастки
2. Заполнение
прессформы пенополистиролом
3. Тепловой
удар, формирование пеномодели
4. Охлаждение и
извлечение пеномодели.
1.
Проектирование и изготовление технологической оснастки
В зависимости от сложности детали, пеномодели могут быть цельные или
составные (состоящие из нескольких частей), которые впоследствии склеиваются
специальным клеем. Если пеномодель составная, то для каждой части
изготавливается прессформа, и каждая часть формуется отдельно.
Поэтому при проектировании технологической оснастки (прессформы) для
изготовления пеномоделей проводится анализ с целью определения ключевых
моментов:
- цельная пеномодель или составная;
- определение оптимальной плоскости разъема;
- определение припусков и формовочных уклонов.
Так же при проектировании необходимо учитывать и другие немаловажные
факторы:
- коэффициент усадки пеномодели и металла (сплава), из которого будет
изготовлена отливка;
- количество и расположение отверстий для подачи пара и отвода воздуха (венты,
дюзы);
- количество и расположение пневмозагрузчиков (дозаторов);
- расположение системы выталкивания.
2. Заполнение
прессформы пенополистиролом
Заполнение полости прессформы пенополистиролом может осуществляться
вручную либо же с помощью пневмозагрузчиков (дозаторов). Дозатор
представляет собой цилиндр, внутри которого имеется шток с поршнем. Поршень,
перемещаясь, обеспечивает 2 рабочих положения дозатора: «открыто» и «закрыто».
Так же у дозатора имеются несколько подводящих штуцеров: подачи сырья, открытия,
закрытия. Подавая давление на штуцер открытия, поршень перемещается в рабочее
положение «открыто».
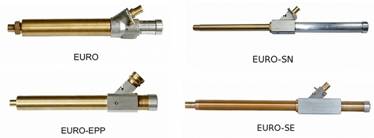
Различные типы пневмозагрузчиков.
Если в системе подачи сырья имеется нагнетатель, то начинается
задувка пенополистирола в полость прессформы. Если в системе нет принудительного
нагнетателя, то используют пневмозагрузчики, у которых имеется
дополнительный штуцер. Подавая давление на этот штуцер, в дозаторе возникает
разрежение, и пенополистирол засасывается из емкости в полость прессформы. По
окончании заполнения прессформы, подается давление на штуцер закрытия, тем самым
перемещая поршень в положение «закрыто».
Использование пневмозагрузчиков ускоряет и упрощает стадию заполнения,
так же обеспечивается точная порционность.
3.
Тепловой удар, формирование пеномодели
Метод теплового удара заключается в следующем: теплоноситель, как
правило это перегретый пар с температурой 105-115°С, поступая в полость
прессформы, нагревает гранулы пенополистирола, которые в свою очередь,
расширяясь, заполняют все пустоты прессформы, приобретая очертания будущей
детали. Пар проникает в полость прессформы через венты, дюзы.
Венты конструктивно имеют форму цилиндрического стакана высотой
6-10мм. Номинальный диаметр венты варьируется от 2 до 30мм. Высота (толщина)
рабочей части (дна) венты – 2-4мм. Так же, для обеспечения плотной посадки венты
в отверстии прессформы, на наружном диаметре ниже рабочей части имеется накатка
диаметром больше номинального диаметра венты.
Основное назначение венты – обеспечение отвода воздуха из полости
прессформы в момент заполнения пенополистиролом и подача перегретого пара в
процессе формования пеномодели, поэтому в рабочей части венты имеются отверстия
или пазы (в зависимости от исполнения). Тем самым венты разделяются на 2 типа:
- венты с пазами (щелевые венты);
- венты с отверстиями.
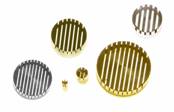
Венты с отверстиями Венты
с пазами
Количество пазов (отверстий) варьируется в зависимости от номинального
диаметра венты. Ширина паза (диаметр отверстия) может быть 0,2-0,8мм. Так же
рабочая часть венты с внутренней стороны может быть усилена дополнительным
кольцом (кольцо усиления). Вента с кольцом усиления выдерживает большее
давление, оказываемое пенополистиролом в процессе формования пеномодели.
Еще одним типом вент являются глухие венты. Они предназначены для
закрытия отверстий, по каким либо причинам непригодных для установки вент с
отверстиями или пазами.
В зависимости от области применения (прессформы ЛГМ, стержневые ящики и
т.д.) венты изготавливают из алюминия, латуни, стали.
4. Охлаждение и извлечение пеномодели.
Перед раскрытием и извлечением пеномодели из полости прессформы,
пеномодель и саму прессформу необходимо охладить. Для этого с тыльной стороны
прессформы на формовочной машине размещают систему трубопроводов с форсунками,
через которые, распыляя воду на прессформу, и происходит охлаждение.
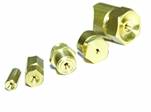
Форсунки системы охлаждения
В зависимости от габаритов пеномодели, от расположения и возможностей
оборудования, пеномодель извлекают несколькими способами:
- вручную, т.е. оператор руками осторожно извлекает пеномодель из
полости прессформы.
- пеномодель при раскрытии формовочной машины сама падает в
деталеприемник.
- с помощью системы выталкивания. Система выталкивания может быть
пневматической, либо механической, а так же совмещенной с пневмозагрузчиком.
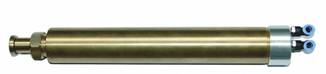
Пневматический выталкиватель
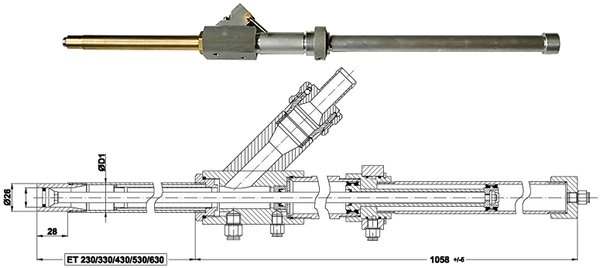
Пневмозагрузчик AVN 5070-AW 50.70.00.00
Приведем один из вариантов использования механической системы
выталкивания: во время раскрытия формовочной машины плита толкателей, двигаясь,
давит на заднюю поверхность толкателя, при этом, пружина, которая находится на
толкателе, сжимается. Толкатель, перемещаясь, упирается в пеномодель и
выталкивает ее из прессформы. Рабочей поверхностью, контактирующей с моделью,
является тарелка толкателя, поэтому, чтобы избежать повреждения модели («проминание
модели»), диаметр толкателя значительно больше (следовательно, и площадь
контактируемой поверхности), чем диаметр толкателя. Тарелки толкателя могут быть
выполнены как из стали нержавеющей, так и из бронзы.
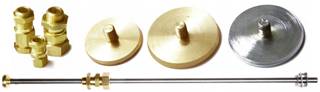
Комплектующие механической системы выталкивания
Когда формовочная машина закрывается для следующего цикла изготовления
пеномоделей, толкатели возвращаются в первоначальное положение за счет возврата
пружины в несжатое состояние. Фиксатор пружины, который представляет собой
установочное/стопорное кольцо + винт шестигранный, предназначен для
регулирования силы сжатия пружины, а также предотвращает соскакивание пружины с
толкателя.
Из-за того, что в процессе изготовления используется пар, готовым
пеномоделям необходимо пройти сушку либо на открытом воздухе, либо в специальных
сушильных камерах.
А.Б.
Ефимов
a-b-efimov@yandex.ru |